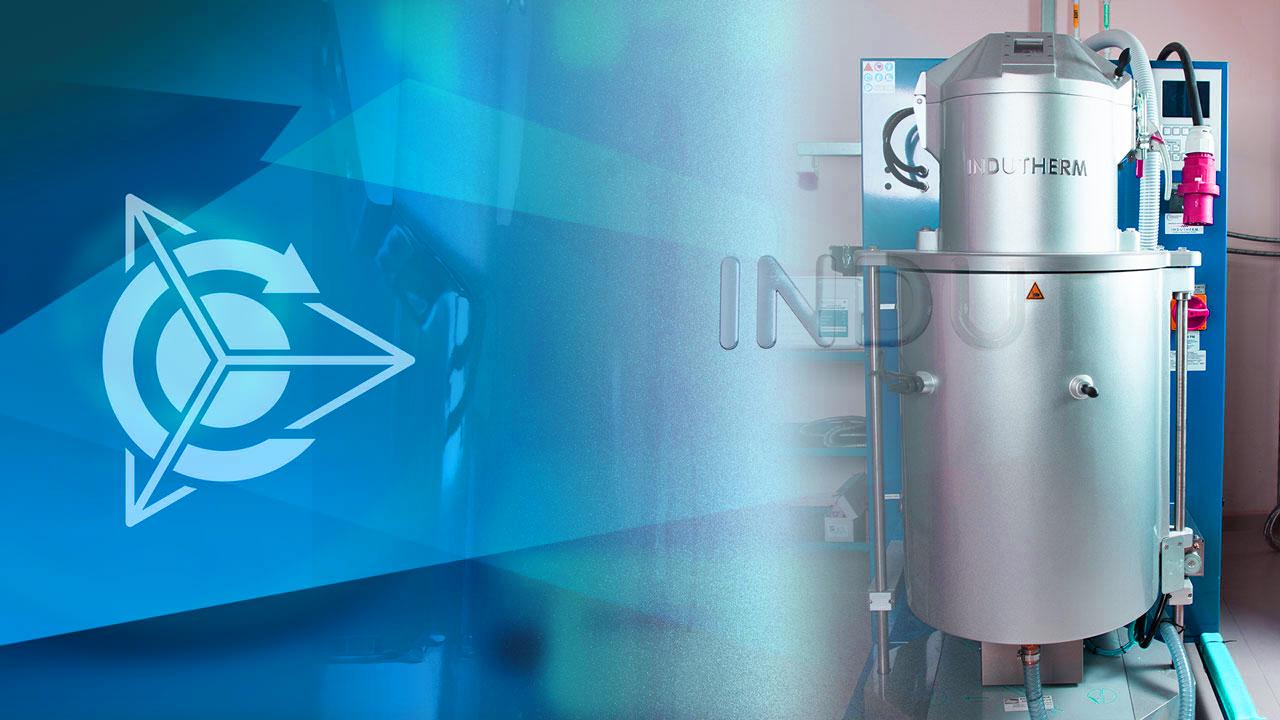
Work routine: the first start of the casting equipment
“SovElMash” has conducted the long-awaited start of the die casting machine.
When there is a casting machine at the production site, the amount of various waste materials is minimized and they can be now be remelted for secondary use and making workpieces, which, in its turn, reduces the product cost.
The workpieces can be cast in high-precision size with minimal machining, which allows to make the production process less costly.
Another advantage is no need to involve contractors for casting the required parts, it is now possible to do that at our own casting shop.
Metal performance features do not change after casting, this material is not subject to contamination. The casting process itself, thanks to the nitrogen plant, will be carried out in oxygen-free environment that doesn’t allow oxide formation.
While the specialists are working on the casting machine, Igor Korkhov received the sine-wave controller from the “Velomastera” portal. This controller will replace the “faulty” Kelly for testing the Chinese hub motor.
With the new controller, we managed to get proper graphs that proved the parameters stated by the manufacturers for this motor.
Further, for comparing the performance features, the BLDC motor will also be tested with a “SovElMash” controller.